在全球能源转型背景下,太阳能光伏组件需直面严苛自然环境的长期考验。离型膜作为组件封装工艺中的功能性材料,其耐候性直接关系到光伏组件的使用寿命和发电效率。本文从离型膜的功能定位出发,结合光伏组件的工作环境,解析其耐候性表现及技术突破方向。
功能定位:光伏组件中的“临时守护者”
离型膜在光伏组件生产中主要应用于封装胶膜(如EVA、POE)的层压工艺。在层压前,它作为胶膜的临时载体,确保胶膜平整无褶皱;层压完成后,需通过特定工艺(如紫外光照射或机械剥离)从胶膜表面脱离。这一过程中,离型膜需具备两大核心能力:一是与胶膜表面低黏附性,确保易剥离;二是在层压高温(通常140-160℃)下不残留胶质、不变形,避免污染胶膜或组件内部结构。
耐候性挑战:从生产到服役的全周期考验
光伏组件的服役周期长达25年以上,离型膜的耐候性需覆盖“生产-运输-安装-运行”全链条:
高温高湿环境:组件在热带地区运行时,封装胶膜长期处于85℃/85%RH的湿热条件,离型膜残留的微量化学物质可能迁移到胶膜表面,引发胶膜黄变或脱层。研究表明,耐候性差的离型膜会导致胶膜透光率下降3%-5%,直接影响组件发电效率。
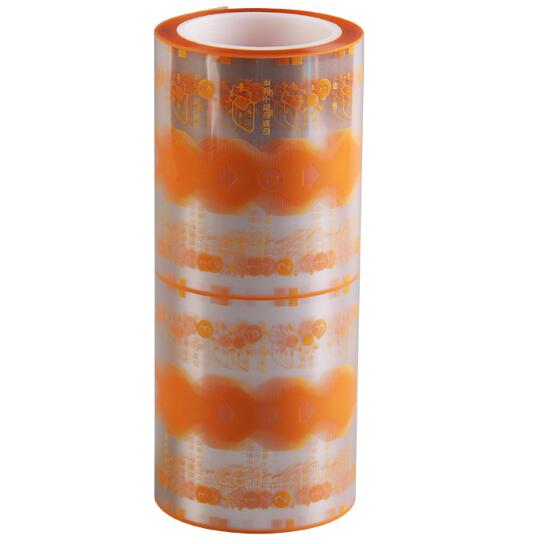
紫外线辐射:高原或沙漠地区紫外线强度超100kWh/m²/年,普通离型膜的聚合物基材(如PET)易发生光氧化降解,表面出现裂纹或粉化,剥离时可能划伤胶膜或电池片。
温度循环冲击:昼夜温差大的地区(如我国西北部),组件经历-40℃至85℃的快速温变,离型膜若热膨胀系数与胶膜不匹配,会导致层压后胶膜内部产生微应力,加速老化。
技术突破:材料创新与工艺优化
为应对上述挑战,行业通过材料改性与工艺升级提升离型膜耐候性:
基材升级:采用氟树脂(如PTFE)或纳米改性PET替代传统PET基材。氟树脂具有极低的表面能和优异的紫外稳定性,在UV照射1000小时后仍能保持表面光滑无裂纹;纳米二氧化硅掺杂PET可提升基材的热稳定性,热变形温度提高至200℃以上。
涂层技术:在基材表面涂覆耐候性涂层(如含硅丙烯酸酯),形成致密保护层。实验数据显示,涂覆后的离型膜在湿热老化测试(85℃/85%RH,1000小时)后,剥离力波动范围从±0.8N降至±0.2N,显著提升胶膜界面稳定性。
低析出配方:通过调整离型剂(如硅油)的分子结构,减少小分子添加剂残留。新型硅烷改性离型剂在层压后析出量降低90%,避免了胶膜表面的“雾度”问题,保障透光率>91%。
未来方向:全生命周期可靠性验证
当前研究正从单一性能优化转向全生命周期模拟测试。通过构建“紫外+湿热+温变”多因素加速老化平台,结合AI算法预测离型膜在实际环境中的性能衰减曲线,为材料选型提供数据支撑。此外,开发可回收离型膜(如生物基聚合物基材)也成为绿色光伏产业链的重要课题。
离型膜的耐候性是光伏组件长期可靠运行的“隐形防线”。随着材料科学与工艺技术的持续突破,耐候性更优的离型膜将进一步提升光伏组件的环境适应性和经济性,为全球清洁能源目标提供更坚实的技术保障。